Terminais de latão niquelado estão se tornando uma escolha preferencial para indústrias que dependem de conexões elétricas de alto desempenho, duráveis e resistentes à corrosão. Esses terminais são comumente utilizados em setores que vão do automotivo ao aeroespacial e oferecem vantagens significativas em relação aos seus equivalentes sem revestimento. À medida que as tecnologias evoluem e as indústrias exigem maior confiabilidade, o papel dos terminais de latão niquelado continua a crescer.
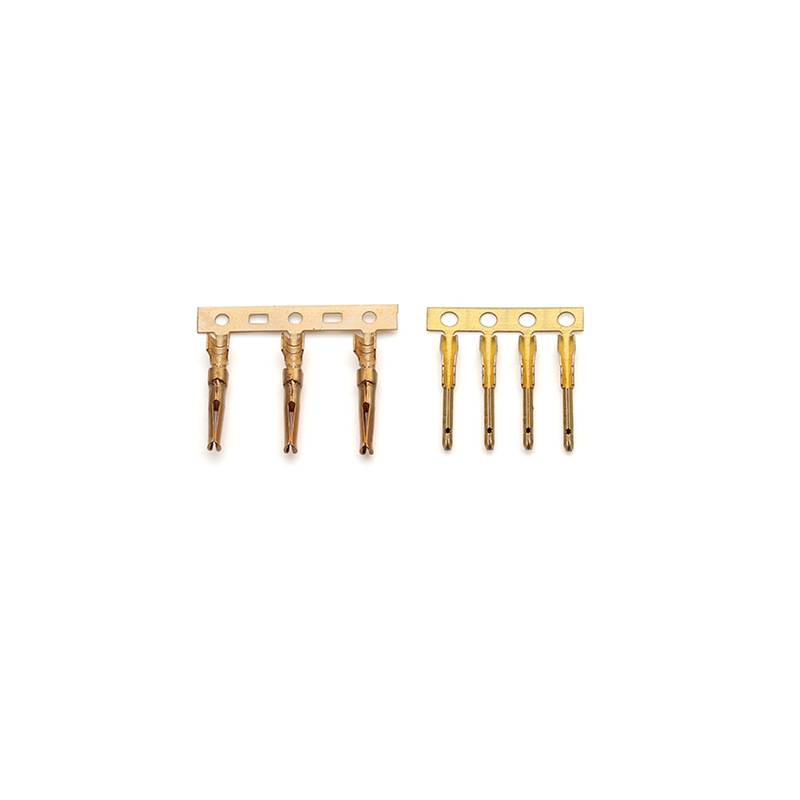
Um dos principais motivos para o uso de terminais de latão niquelado é sua excepcional resistência à corrosão. O revestimento de níquel fornece uma camada protetora que protege o latão subjacente de fatores ambientais, como umidade, salinidade e temperaturas extremas. Essa característica é particularmente valiosa em aplicações automotivas e industriais. Por exemplo, muitos fabricantes de automóveis, incluindo Ford e Toyota, utilizam terminais de latão niquelado nas conexões do compartimento do motor e da bateria. Nesses ambientes, onde o calor e a umidade costumam ser elevados, o revestimento de níquel previne a corrosão, garantindo que os terminais mantenham uma conexão estável ao longo do tempo.
Terminais de latão niquelado também são preferidos em indústrias onde a condutividade elétrica e a confiabilidade a longo prazo são críticas. Embora o latão tenha uma condutividade menor em comparação ao cobre puro, o revestimento de níquel melhora o desempenho geral, aumentando a durabilidade e a resistência à oxidação do terminal. Isso garante que as conexões elétricas permaneçam estáveis, mesmo em ambientes de alta vibração. Um bom exemplo disso pode ser visto no setor aeroespacial, onde esses terminais são usados nos sistemas de fiação de aeronaves comerciais como o Boeing 787. As condições adversas de altas altitudes e temperaturas variáveis tornam a corrosão uma séria preocupação. Ao usar terminais de latão niquelado, a Boeing garante que os sistemas elétricos da aeronave sejam duráveis e confiáveis, reduzindo significativamente o risco de falhas.
The manufacturing process of these terminals also plays a crucial role in their effectiveness. Electroplating is the most common method for applying the nickel coating, providing a uniform and durable finish. The plating thickness is carefully controlled to balance performance and cost. Research from the Journal of Electrochemical Society highlights that nickel plating thicknesses between 5 and 10 microns can increase corrosion resistance by up to 30%. This makes the process cost-effective, as the added durability compensates for the slight increase in manufacturing costs—an important factor in industries where performance outweighs price.
Nickel plated brass terminals are also known for their mechanical properties. The nickel coating adds hardness to the brass, making these terminals more resistant to wear and tear. This is especially useful in applications where frequent connections and disconnections occur, such as in industrial automation or consumer electronics. Companies like Siemens have adopted nickel plated brass terminals in their automated control systems to ensure that their connectors withstand frequent use without deteriorating. Tests published in the Wear Journal show that nickel plated brass terminals exhibit 35% more resistance to wear than non-plated alternatives, making them ideal for high-frequency applications.
À medida que as preocupações ambientais se tornam mais proeminentes, terminais de latão niquelado também estão sendo produzidos com foco em questões ecológicas. As empresas estão adotando cada vez mais métodos de niquelagem sem cianeto para reduzir o uso de produtos químicos tóxicos. A Heraeus, por exemplo, foi pioneira em tecnologias de galvanoplastia sem cianeto, permitindo a produção de terminais de latão niquelado de alta qualidade sem impactos ambientais prejudiciais. Essa mudança está alinhada aos padrões regulatórios globais, como a diretiva RoHS da União Europeia, que restringe o uso de certas substâncias perigosas em equipamentos eletrônicos.
The demand for nickel plated brass terminals is not confined to traditional industries. With the rise of electric vehicles (EVs), the need for robust, corrosion-resistant electrical components is more significant than ever. In electric vehicles, where the performance of electrical systems is crucial to the vehicle’s efficiency and safety, manufacturers like Tesla are turning to nickel plated brass terminals for their battery management systems and electric drivetrains. According to the Electric Vehicle Market Report, the demand for such terminals is expected to increase by more than 20% by 2025, as the EV market grows rapidly.
Concluindo, os terminais de latão niquelado oferecem uma combinação de durabilidade, resistência à corrosão e desempenho elétrico que os torna uma escolha superior para diversos setores. Da indústria automotiva e aeroespacial à automação industrial e veículos elétricos, esses terminais desempenham um papel fundamental para garantir a confiabilidade e a longevidade dos sistemas elétricos. À medida que os métodos de produção evoluem e os padrões ambientais se tornam mais rigorosos, o uso de terminais de latão niquelado tende a se expandir cada vez mais, consolidando seu lugar no futuro da tecnologia.